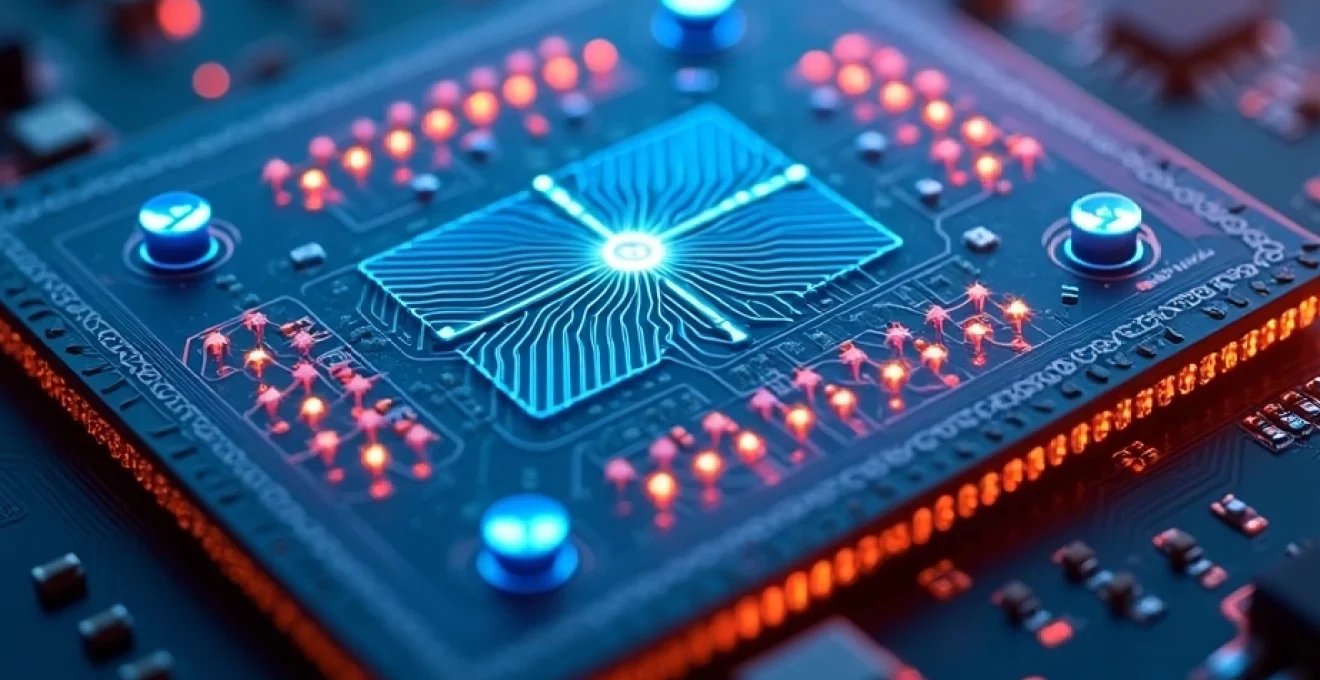
Die rasante Entwicklung der Elektronik treibt die Miniaturisierung von Geräten stetig voran. Im Zentrum dieser Revolution stehen flexible Leiterplatten (FPCBs), die es ermöglichen, elektronische Komponenten in immer kleinere und komplexere Formen zu bringen. Diese biegsamen Schaltungsträger eröffnen völlig neue Möglichkeiten für das Design ultrakompakter und anpassungsfähiger elektronischer Produkte. Von smartwatches bis hin zu medizinischen Implantaten - FPCBs sind der Schlüssel zur Realisierung innovativer Miniaturelektronik, die unser tägliches Leben zunehmend prägt und verändert.
Grundlagen flexibler Leiterplatten-Technologie
Flexible Leiterplatten unterscheiden sich grundlegend von ihren starren Gegenstücken. Sie bestehen aus einem dünnen, biegsamen Substrat, auf dem leitfähige Bahnen aufgebracht sind. Dies ermöglicht es, elektronische Schaltungen in dreidimensionale Formen zu bringen und sie an begrenzte Räume anzupassen. Die Flexibilität wird durch die Verwendung spezieller Polymermaterialien wie Polyimid erreicht, die extreme Biegungen ohne Bruch oder Ermüdung aushalten.
Ein entscheidender Vorteil von FPCBs ist ihre Fähigkeit, Gewicht und Volumen im Vergleich zu starren Leiterplatten drastisch zu reduzieren. Dies macht sie ideal für Anwendungen, bei denen jedes Gramm und jeder Millimeter zählt. Zudem ermöglichen FPCBs dynamische Bewegungen innerhalb eines Geräts, was besonders für Wearables und faltbare Elektronik von Bedeutung ist.
Die Herstellung von FPCBs erfordert spezielle Fertigungstechniken. Anders als bei starren Leiterplatten müssen hier Materialien und Prozesse verwendet werden, die die Flexibilität des Endprodukts gewährleisten. Dies stellt Hersteller vor besondere Herausforderungen, eröffnet aber auch neue Möglichkeiten für innovative Designs.
Materialinnovationen für ultradünne FPCBs
Die kontinuierliche Weiterentwicklung von Materialien ist ein Schlüsselfaktor für die fortschreitende Miniaturisierung von FPCBs. Forscher und Ingenieure arbeiten unermüdlich daran, noch dünnere, flexiblere und robustere Substrate zu entwickeln, die den steigenden Anforderungen moderner Elektronik gerecht werden.
Polyimid-basierte Substrate und ihre Eigenschaften
Polyimid hat sich als das bevorzugte Material für FPCB-Substrate etabliert. Seine herausragenden Eigenschaften wie hohe Temperaturbeständigkeit, chemische Stabilität und mechanische Flexibilität machen es zum idealen Kandidaten für miniaturisierte Elektronik. Neueste Entwicklungen zielen darauf ab, die Dicke von Polyimid-Substraten weiter zu reduzieren, ohne dabei Kompromisse bei der Leistungsfähigkeit einzugehen.
Ein bemerkenswerter Fortschritt ist die Entwicklung von Polyimid-Filmen mit einer Dicke von weniger als 10 Mikrometern. Diese ultradünnen Substrate ermöglichen es, FPCBs zu schaffen, die sich nahtlos in kleinste Räume integrieren lassen. Die Herausforderung besteht darin, die Handhabung und Verarbeitung dieser extrem dünnen Materialien zu optimieren, um eine zuverlässige Massenproduktion zu gewährleisten.
Leitfähige Tinten und Pasten für flexible Schaltungen
Neben den Substraten spielen leitfähige Materialien eine entscheidende Rolle bei der Miniaturisierung von FPCBs. Traditionelle Kupferleiterbahnen stoßen bei extremer Miniaturisierung an ihre Grenzen. Hier kommen innovative leitfähige Tinten und Pasten ins Spiel, die mittels Drucktechniken aufgebracht werden können.
Diese Materialien, oft auf Basis von Silber oder Kohlenstoff-Nanoröhrchen, ermöglichen die Herstellung extrem feiner Leiterbahnen mit Breiten von weniger als 50 Mikrometern. Dadurch lassen sich komplexe Schaltungen auf kleinstem Raum realisieren. Ein zusätzlicher Vorteil ist die Möglichkeit, diese Materialien direkt auf gebogene oder unebene Oberflächen aufzubringen, was völlig neue Designmöglichkeiten eröffnet.
Nanomaterialien zur Verbesserung der Flexibilität
Die Integration von Nanomaterialien in FPCBs stellt einen weiteren Meilenstein in der Miniaturisierung dar. Graphen und Kohlenstoff-Nanoröhrchen bieten eine einzigartige Kombination aus elektrischer Leitfähigkeit und mechanischer Flexibilität. Diese Materialien können in extrem dünnen Schichten aufgebracht werden und halten selbst starken Verformungen stand.
Forscher arbeiten daran, Nanomaterialien in Polyimid-Substrate zu integrieren, um deren elektrische und mechanische Eigenschaften weiter zu verbessern. Das Resultat sind Hybridsubstrate, die eine noch höhere Packungsdichte bei gleichzeitiger Steigerung der Flexibilität ermöglichen. Diese Entwicklung könnte den Weg für eine neue Generation von ultradünnen und hochleistungsfähigen FPCBs ebnen.
Entwicklung von streckbaren Elektroniksubstraten
Die nächste Evolutionsstufe in der FPCB-Technologie sind streckbare Elektroniksubstrate. Diese Materialien gehen über die reine Biegsamkeit hinaus und können sich dehnen und zusammenziehen, ohne ihre elektrischen Eigenschaften zu verlieren. Elastomere wie PDMS (Polydimethylsiloxan) werden mit leitfähigen Materialien kombiniert, um Substrate zu schaffen, die sich an dynamische Formen anpassen können.
Streckbare Elektronik eröffnet völlig neue Anwendungsfelder, insbesondere im Bereich der Wearables und medizinischen Implantate. Stellen Sie sich elektronische Haut vor, die sich nahtlos an die Körperkonturen anpasst oder Implantate, die mit dem Gewebe mitwachsen können. Diese Technologie steht noch am Anfang, zeigt aber enormes Potenzial für die Zukunft der miniaturisierten Elektronik.
Designstrategien für Miniaturisierung mit FPCBs
Die Miniaturisierung von Elektronik durch FPCBs erfordert innovative Designansätze, die weit über traditionelle Leiterplattenlayouts hinausgehen. Designer müssen den dreidimensionalen Raum optimal nutzen und dabei die einzigartigen Eigenschaften flexibler Materialien berücksichtigen.
3D-Faltungstechniken für kompakte Elektronik
Eine der effektivsten Strategien zur Miniaturisierung ist die Nutzung von 3D-Faltungstechniken. Dabei wird die flexible Leiterplatte so gestaltet, dass sie sich präzise in kompakte dreidimensionale Formen falten lässt. Dies ermöglicht es, die verfügbare Oberfläche maximal auszunutzen und gleichzeitig das Volumen des Geräts zu minimieren.
Designer entwickeln komplexe Faltmuster, die es erlauben, mehrere Funktionsebenen in einem einzigen FPCB zu integrieren. Durch geschickte Anordnung der Komponenten und Leiterbahnen können Bereiche des FPCBs übereinander gefaltet werden, ohne dass es zu Kurzschlüssen oder Interferenzen kommt. Diese Technik findet besonders in der Entwicklung von kompakten Smartphones und Wearables Anwendung.
Mehrlagige flexible Leiterplatten-Architekturen
Um die Packungsdichte weiter zu erhöhen, setzen Designer zunehmend auf mehrlagige FPCB-Architekturen. Ähnlich wie bei starren Multilayer-Leiterplatten werden hier mehrere Schichten flexibler Substrate übereinander laminiert. Dies ermöglicht es, komplexe Schaltungen auf engstem Raum unterzubringen.
Die Herausforderung bei mehrlagigen FPCBs liegt in der Beibehaltung der Flexibilität bei gleichzeitiger Gewährleistung zuverlässiger Verbindungen zwischen den Schichten. Innovative Verbindungstechnologien wie lasergebohrt Microvias spielen hier eine entscheidende Rolle. Sie ermöglichen präzise Verbindungen zwischen den Lagen, ohne die Gesamtflexibilität des Aufbaus zu beeinträchtigen.
Hochdichte Verbindungstechnologien für FPCBs
Die Miniaturisierung von FPCBs erfordert auch neue Ansätze in der Verbindungstechnik. Traditionelle Löttechniken stoßen bei extrem feinen Strukturen an ihre Grenzen. Hier kommen fortschrittliche Bondingverfahren zum Einsatz, die es ermöglichen, Komponenten direkt auf die flexiblen Substrate aufzubringen.
Technologien wie Flip-Chip-Bonding und Anisotropic Conductive Film (ACF) ermöglichen ultrafeine Verbindungen mit Abständen von weniger als 100 Mikrometern. Diese Methoden reduzieren nicht nur den Platzbedarf, sondern verbessern auch die elektrische Leistung durch kürzere Signalwege. Zudem sind sie besser geeignet für die dynamischen Belastungen, denen FPCBs in vielen Anwendungen ausgesetzt sind.
Die Kombination aus innovativen Materialien, 3D-Faltungstechniken und hochdichten Verbindungstechnologien ermöglicht es, elektronische Geräte zu entwickeln, die noch vor wenigen Jahren als undenkbar galten.
Fertigungsprozesse für Mikro-FPCBs
Die Herstellung von miniaturisierten FPCBs stellt hohe Anforderungen an die Fertigungsprozesse. Traditionelle Methoden der Leiterplattenherstellung müssen angepasst und verfeinert werden, um die extrem feinen Strukturen und dünnen Materialien zu verarbeiten.
Ein Schlüsselprozess ist die Photolithographie, die es ermöglicht, ultrafeine Leiterbahnstrukturen zu erzeugen. Moderne Anlagen können Strukturen mit einer Auflösung von weniger als 10 Mikrometern realisieren. Dies erfordert jedoch höchste Präzision und Sauberkeit im Fertigungsumfeld.
Für die Handhabung der dünnen und flexiblen Substrate kommen spezielle Halte- und Transportsysteme zum Einsatz. Diese müssen die Materialien schonend behandeln, um Verformungen oder Beschädigungen zu vermeiden. Gleichzeitig müssen sie eine präzise Positionierung für nachfolgende Prozessschritte gewährleisten.
Die Qualitätskontrolle spielt bei der Fertigung von Mikro-FPCBs eine entscheidende Rolle. Hochauflösende optische Inspektionssysteme und elektrische Testverfahren stellen sicher, dass jede Leiterplatte den strengen Anforderungen entspricht. Selbst kleinste Defekte können die Funktion des Endprodukts beeinträchtigen.
Ein weiterer wichtiger Aspekt ist die Reinraumfertigung. Je kleiner die Strukturen werden, desto empfindlicher reagieren sie auf Verunreinigungen. Viele Hersteller von Mikro-FPCBs investieren daher in hochmoderne Reinraumanlagen, um eine kontaminationsfreie Produktion zu gewährleisten.
Anwendungsfelder miniaturisierter FPCB-Elektronik
Die Miniaturisierung durch FPCBs eröffnet ein breites Spektrum an innovativen Anwendungen in verschiedenen Branchen. Von Konsumerelektronik bis hin zu medizinischen Geräten revolutionieren miniaturisierte FPCBs die Art und Weise, wie wir Elektronik entwerfen und nutzen.
Wearable-Technologie und Smart Clothing
Im Bereich der Wearables spielen miniaturisierte FPCBs eine zentrale Rolle. Sie ermöglichen die Integration von Elektronik in Kleidungsstücke und Accessoires, ohne deren Tragekomfort zu beeinträchtigen. Smartwatches, Fitness-Tracker und intelligente Textilien profitieren von der Flexibilität und Kompaktheit dieser Technologie.
Ein faszinierendes Beispiel sind intelligente Kontaktlinsen, die dank ultradünner FPCBs mit Sensoren und Displays ausgestattet werden können. Diese Geräte könnten in Zukunft Gesundheitsdaten in Echtzeit erfassen oder sogar Augmented-Reality-Inhalte direkt ins Sichtfeld des Trägers projizieren.
Medizinische Implantate und Biosensoren
In der Medizintechnik ermöglichen miniaturisierte FPCBs die Entwicklung hochkomplexer Implantate und Biosensoren. Moderne Herzschrittmacher und Neurostimulatoren nutzen flexible Schaltungen, um sich optimal an die Anatomie des Patienten anzupassen. Dies verbessert nicht nur den Tragekomfort, sondern auch die Langzeitstabilität der Implantate.
Biosensoren auf Basis von FPCBs können direkt auf der Haut getragen werden und kontinuierlich verschiedene Gesundheitsparameter überwachen. Die Flexibilität des Materials gewährleistet dabei einen guten Kontakt zur Haut und erhöht die Messgenauigkeit.
Faltbare Smartphones und rollbare Displays
Die Vision von faltbaren Smartphones und rollbaren Displays wird durch miniaturisierte FPCBs Realität. Diese Technologie ermöglicht es, flexible Displaymodule mit der notwendigen Elektronik zu verbinden, ohne die Biegsamkeit des Geräts zu beeinträchtigen.
Designer nutzen komplexe FPCB-Layouts, die es ermöglichen, die Displayfläche zu vergrößern oder zu verkleinern, ohne die Funktionalität zu beeinträchtigen. Ein Beispiel dafür sind die sogenannten "Z-Fold"-Designs, bei denen das FPCB in mehreren Ebenen gefaltet wird, um ein kompaktes Gerät zu schaffen, das sich bei Bedarf entfalten lässt.
Internet der Dinge (IoT) Mikrogeräte
Die Vision des Internet der Dinge wird durch miniaturisierte FPCBs greifbar. Winzige Sensoren und Kommunikationsmodule können dank dieser Technologie in alltägliche Gegenstände integriert werden, ohne deren Form oder Funktion zu beeinträchtigen.
Ein spannendes Anwendungsgebiet sind intelligente Staubpartikel - mikroskopisch kleine Sensoren, die in der Umwelt verteilt werden können, um Daten zu sammeln. Diese "Smart Dust"-Geräte nutzen flexible Schaltungen, um auf kleinstem Raum Sensoren, Prozessoren und Kommunikationsmodule zu integrieren.
Auch in der Industrie 4.0 spielen miniaturisierte IoT-Geräte eine wichtige Rolle. Flexible Sensoren können direkt auf Maschinenteilen oder in schwer zugänglichen Bereichen angebracht werden, um Betriebsdaten in Echtzeit zu erfassen und zu übermitteln. Dies ermöglicht eine präzisere Überwachung und vorausschauende Wartung industrieller Anlagen.
Herausforderungen und Zukunftsperspektiven der FPCB-Miniaturisierung
Trotz der beeindruckenden Fortschritte in der FPCB-Technologie stehen Entwickler und Hersteller weiterhin vor Herausforderungen. Eine der größten ist die Zuverlässigkeit bei extremer Miniaturisierung. Je kleiner die Strukturen werden, desto anfälliger sind sie für Fehler und Ausfälle. Die Entwicklung von robusten Designs und Fertigungsprozessen, die auch unter anspruchsvollen Bedingungen zuverlässig funktionieren, bleibt eine zentrale Aufgabe.
Ein weiteres Problemfeld ist die Wärmeentwicklung in miniaturisierten Geräten. Die hohe Packungsdichte elektronischer Komponenten kann zu lokalen Überhitzungen führen. Innovative Kühlkonzepte und thermisch optimierte Materialien sind gefragt, um die Leistungsfähigkeit und Lebensdauer der Geräte zu gewährleisten.
Die Integration von Energieversorgungssystemen stellt eine weitere Herausforderung dar. Wie können wir Batterien oder Energieerntetechnologien in ultrakompakte Designs integrieren, ohne die Flexibilität zu beeinträchtigen? Hier arbeiten Forscher an Lösungen wie flexiblen Batterien oder der Integration von Solarzellen direkt in die FPCB-Struktur.
Die Zukunft der FPCB-Miniaturisierung liegt in der ganzheitlichen Integration von Funktionalität, Energieversorgung und Sensorik in flexible, anpassungsfähige Systeme.
Blicken wir in die Zukunft, so zeichnen sich faszinierende Entwicklungen ab. Die Konvergenz von FPCBs mit anderen Technologien wie 3D-Druck und Nanotechnologie eröffnet neue Möglichkeiten. Stellen Sie sich vor, wir könnten flexible elektronische Strukturen direkt auf oder sogar in Objekte drucken. Oder denken Sie an selbstheilende Schaltungen, die kleine Risse oder Beschädigungen automatisch reparieren können.
Ein weiterer vielversprechender Ansatz ist die Entwicklung von biokompatiblen und biologisch abbaubaren FPCBs. Diese könnten nicht nur in medizinischen Implantaten zum Einsatz kommen, sondern auch das Problem der Elektronikabfälle adressieren. Stellen Sie sich Geräte vor, die nach ihrer Nutzungsdauer einfach umweltfreundlich abgebaut werden können.
Die fortschreitende Miniaturisierung durch FPCBs wird unsere Interaktion mit Technologie grundlegend verändern. Von unsichtbaren, in die Umgebung integrierten Sensoren bis hin zu nahtlos in unseren Körper eingebetteten medizinischen Geräten - die Grenzen zwischen Mensch, Maschine und Umwelt werden zunehmend verschwimmen.
Abschließend lässt sich sagen, dass die Miniaturisierung durch flexible Leiterplatten eine Schlüsseltechnologie für die Zukunft der Elektronik darstellt. Sie ermöglicht nicht nur kompaktere und leistungsfähigere Geräte, sondern eröffnet völlig neue Anwendungsfelder und Designmöglichkeiten. Die Herausforderungen sind beträchtlich, aber das Potenzial dieser Technologie, unser Leben zu verbessern und neue technologische Horizonte zu erschließen, ist enorm. Während wir weiter an den Grenzen des technisch Machbaren arbeiten, können wir uns auf eine Zukunft freuen, in der Elektronik nahtlos in unseren Alltag integriert ist - flexibel, unsichtbar und allgegenwärtig.